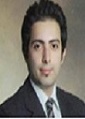
Shahab Kashani Rahimi
University of Southern Mississippi, USA
Title: Graphene/hydroxyl ethyl cellulose aerogels for deformation sensing
Biography
Biography: Shahab Kashani Rahimi
Abstract
Graphene, a one-atom-thick 2-dimensional carbon nanomaterial has received considerable attention from researchers in various disciplines due to its exceptional thermal, mechanical and electrical properties owing to its unique long-ranged π conjugated structure. Due to its unique structure and properties, it has found numerous applications ranging from polymer composites, electronics, and biomedical devices to energy storage and sensors. One of the interesting applications of graphene is in flexible superelastic deformation/strain sensors. For this purpose, flexible porous graphene-based superstructures are good candidates due to their elasticity, high surface area, electrical conductivity, and low density. However, due to severe aggregation of graphene platelets, these graphene aerogels (GAs) tend to be brittle with irrecoverable deformation and properties. In order to address this issue, a number of different polymers such as polyacrylic acid and sodium alginate have been used as a component in conjunction with graphene. However, a systematic study focused on the analysis of the aerogel component variables and its subsequent effects on final structure and properties is still needed in order to get a better understanding of the processing-structure-property relationships of such aerogels. This study reports on the preparation of a series of graphene aerogels in combination with hydroxyl ethyl cellulose (HEC) building block. The effects of the molecular weight of the HEC and crosslinking of the HEC phase with glutaraldehyde and aerogel composition on the structure and properties of the final aerogels are presented. It was found that the use of low molecular weight HEC (92kDa) at the appropriate concertation can develop honey-comb porous structure with superior mechanical properties, high porosity, rapid deformation response, as well as, significantly lower deformation hysteresis.